Check out our new Substack, Merchandise Trade With Legion
What are the different kinds of refractories?
Refractories are specialized materials designed to withstand extreme temperatures in industrial processes. This blog explores different types of refractories—bricks, castables, mortars, ramming mass, and ceramic fibers—highlighting their properties, applications, and benefits. Each type plays a crucial role in industries like steel, glass, and cement, ensuring efficiency, safety, and durability in high-temperature environments.
ENGLISH
5 min read
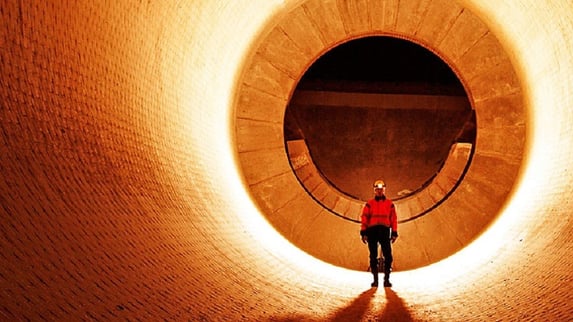
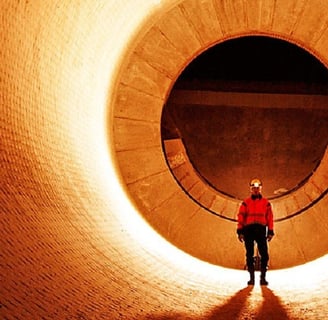
Refractories are materials that can withstand extremely high temperatures without melting or breaking down. These specialized materials are crucial in various industrial processes, particularly those involving high heat, such as in the production of steel, glass, cement, and ceramics.
Refractories are designed to maintain their strength, stability, and chemical integrity under the severe conditions they are exposed to, including extreme temperatures, corrosive chemicals, and mechanical stress.
The primary function of refractories is to act as a protective barrier between the high-temperature environment and the structures that need to be shielded, such as furnace linings, kilns, incinerators, and reactors. By doing so, they help in ensuring the efficiency, safety, and longevity of these industrial systems.
Kinds of Refractories
Refractories come in various forms, each designed for specific applications and conditions. The main types include bricks, castables, mortars, ramming mass, and ceramic fibers. Let's explore each type, along with their properties, applications, and benefits.
Bricks
Properties: Refractory bricks, also known as firebricks, are one of the most common forms of refractories. These bricks are made from various materials, including alumina, silica, magnesia, and other compounds that can withstand high temperatures. They are known for their high thermal conductivity, strength, and resistance to thermal shock, making them suitable for use in environments with fluctuating temperatures.
Applications: Refractory bricks are widely used in the construction of furnaces, kilns, incinerators, and reactors. They serve as the lining for these structures, protecting them from the intense heat generated during industrial processes. Common applications include:
Blast furnaces: For iron and steel production.
Glass furnaces: In the glassmaking industry.
Cement kilns: For the production of cement.
Incinerators: For waste disposal at high temperatures.
Benefits:
Durability: Refractory bricks can last for many years, even under extreme conditions.
Thermal stability: They maintain their integrity even with sudden temperature changes.
Customization: Available in various shapes and sizes, they can be tailored to fit specific industrial needs.
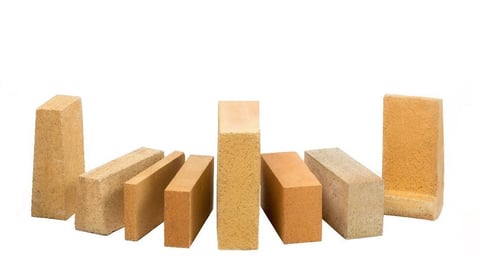
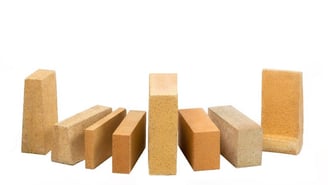
Castables
Properties: Refractory castables are a type of refractory material that comes in an unshaped form. They consist of a mixture of aggregates, binders, and additives, which can be poured or cast into molds to form solid shapes after curing. Castables are known for their excellent mechanical strength, thermal insulation properties, and resistance to abrasion.
Applications: Castables are versatile and can be used in various industrial settings. They are particularly useful in situations where the refractory lining needs to be installed in situ, such as:
Furnace linings: Where complex shapes are required.
Boilers: In power plants to provide thermal insulation.
Ladle linings: In steelmaking processes to hold molten metal.
Repair work: On existing refractory linings, where bricks or preformed shapes may not be practical.
Benefits:
Flexibility: Can be shaped to fit complex geometries.
Ease of installation: Can be cast directly at the site, reducing installation time.
High strength: Provides a robust and durable lining capable of withstanding harsh conditions.
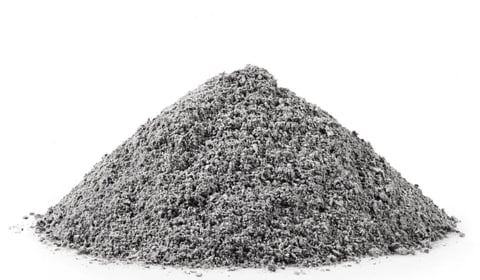
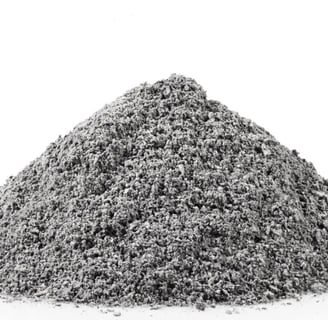
Mortars
Properties: Refractory mortars are specialized bonding agents used to join refractory bricks and other materials. They are composed of fine aggregates, binders, and other additives that give them the necessary properties to withstand high temperatures and chemical attacks. Mortars are designed to have high adhesive strength, thermal resistance, and corrosion resistance.
Applications: Refractory mortars are primarily used in conjunction with refractory bricks. They ensure that the bricks are securely bonded together, preventing the penetration of gases, slags, or other harmful substances. Key applications include:
Furnace linings: To bond firebricks in high-temperature furnaces.
Chimneys: For lining flue gas paths.
Kiln linings: In the ceramics industry, where precise and durable construction is essential.
Benefits:
Strong bonding: Provides a tight seal between refractory bricks, enhancing the overall stability of the structure.
Thermal compatibility: Matches the expansion and contraction rates of the bricks, preventing cracks and gaps.
Ease of application: Mortars can be easily applied, even in hard-to-reach areas.
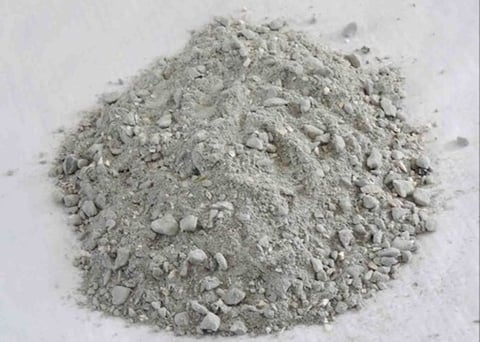
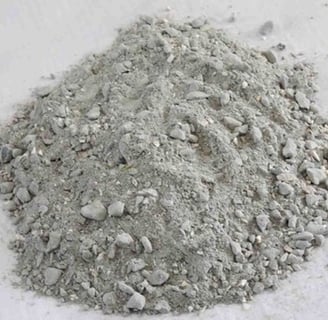
Ramming Mass
Properties: Ramming mass, also known as ramming mix, is an unshaped refractory material used to create monolithic linings. It consists of graded refractory aggregates, binders, and additives. Ramming mass is applied by ramming (compacting) it into place, forming a dense and cohesive lining that can withstand high temperatures, mechanical stress, and chemical attack.
Applications: Ramming mass is used in several high-temperature industrial processes where monolithic linings are preferred over brick or castable linings. Common applications include:
Induction furnaces: For melting metals, particularly in the steel and foundry industries.
Troughs and runners: In the casting of molten metal.
Coreless furnaces: For metal melting, where a strong and impermeable lining is essential.
Benefits:
Seamless lining: Provides a continuous and crack-free surface, reducing the risk of leaks.
High density: Ensures durability and resistance to wear.
Thermal and chemical resistance: Withstands aggressive conditions, including exposure to slags and molten metal.
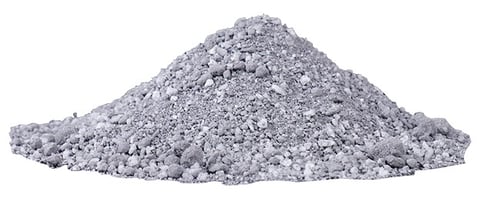
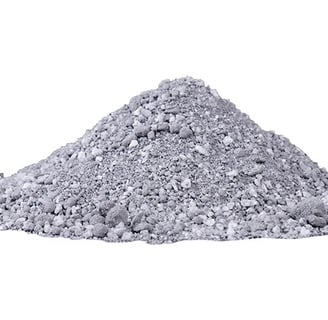
Ceramic Fibers
Properties: Ceramic fibers are lightweight, flexible refractory materials made from high-purity aluminosilicate materials. These fibers are available in various forms, such as blankets, boards, and paper. Ceramic fibers are known for their excellent thermal insulation properties, low thermal conductivity, and resistance to thermal shock.
Applications: Ceramic fibers are widely used in applications where lightweight and highly efficient thermal insulation is required. Key applications include:
Furnace linings: For energy-saving insulation.
Kiln car insulation: In the ceramics industry.
High-temperature gasketing: In furnaces and other thermal equipment.
Fire protection: As a barrier in fireproofing systems.
Benefits:
Lightweight: Reduces the overall weight of the structure, leading to energy savings.
Flexible: Can be easily cut and shaped to fit complex geometries.
Excellent insulation: Provides superior thermal insulation, reducing heat loss and energy consumption.
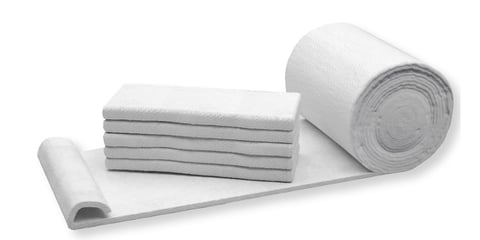
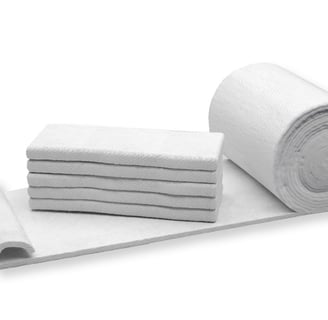
Conclusion
Refractories play an indispensable role in various high-temperature industrial processes. Whether in the form of bricks, castables, mortars, ramming mass, or ceramic fibers, each type of refractory material has its unique properties, applications, and benefits.
These materials are critical in ensuring the efficiency, safety, and longevity of industrial systems, from steel production and glassmaking to power generation and waste incineration.
Understanding the different kinds of refractories and their applications allows industries to select the most appropriate materials for their specific needs, ensuring optimal performance and longevity of their high-temperature equipment.
As technology advances and industrial processes evolve, the development and application of refractory materials will continue to be a vital component of industrial innovation and sustainability.