Check out our new Substack, Merchandise Trade With Legion
Refractories in Boilers and Incinerators: How & Where They Are Used
ENGLISH
3 min read
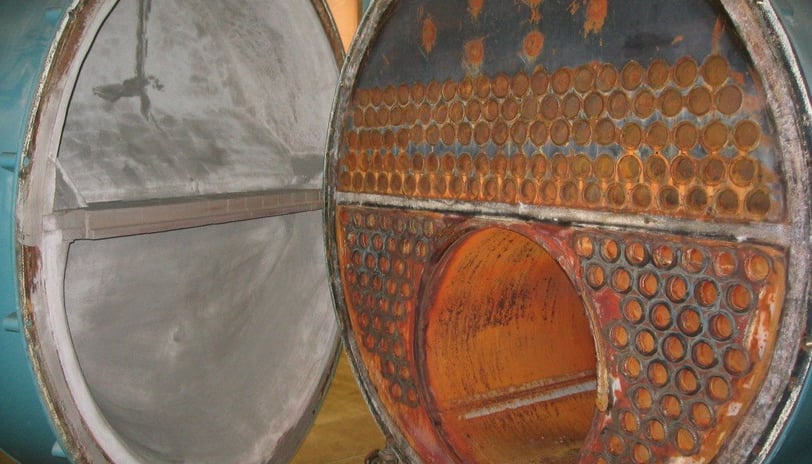
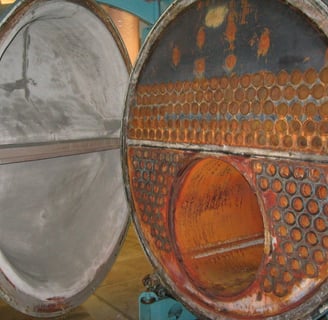
When we think about the incredible machinery that powers our industrial world, we often focus on the big names—engines, turbines, and advanced control systems. However, there’s an equally crucial component that works tirelessly behind the scenes to keep these systems running efficiently: refractories. Let’s explore the role and importance of refractories in boilers and incinerators and understand why they are essential to high-temperature systems.
What Are Refractories?
Refractories are heat-resistant materials designed to withstand extreme temperatures and harsh environments.
Composed mainly of ceramics and minerals, refractories are engineered to maintain their strength, stability, and structural integrity even under intense thermal and chemical stress.
Their primary role is to protect other materials and structures from high temperatures and corrosive conditions.
Refractories in Boilers
Boilers are critical components in many industries, providing essential heat for various processes. Inside a boiler, refractories are used to line the inner walls of the combustion chamber. This setup serves a dual purpose:
1. Protection Against Heat: The combustion of fuel generates extremely high temperatures. Without refractories, the metal structures of the boiler would quickly degrade under such intense heat. Refractories act as a protective barrier, ensuring that the boiler remains structurally sound and operational.
2. Enhanced Heat Transfer: Refractories help in optimizing heat transfer within the boiler. By efficiently managing the heat generated, they contribute to the overall efficiency of the boiler, ensuring that energy is used effectively and that fuel consumption is optimized.
Types of Refractories Used in Boilers
1. Fireclay Bricks: These are versatile and used for general-purpose applications. They offer good resistance to thermal shock and are cost-effective.
2. High Alumina Bricks: These refractories are designed for areas with higher temperature demands. They have a higher alumina content, which makes them more resistant to heat and thermal shock.
3. Insulating Bricks: These refractories provide thermal insulation, which helps in maintaining temperature control and improving energy efficiency within the boiler.
Each type of refractory is selected based on specific requirements such as temperature range, thermal conductivity, and the nature of the fuel being used.
Refractories in Incinerators
Incinerators operate at even higher temperatures than boilers, often exceeding 1000°C. In these high-temperature environments, refractories play a crucial role:
1. Protection Against Thermal Shock: Incinerators handle the combustion of various types of waste, which can lead to sudden and extreme temperature fluctuations. Refractories protect the incinerator structure from these thermal shocks, ensuring long-term durability.
2. Resistance to Chemical Corrosion: The combustion of waste materials can produce corrosive by-products that attack the structural components of the incinerator. Refractories resist these chemical attacks, maintaining the integrity of the incinerator.
Types of Refractories Used in Incinerators
1. Silicon Carbide Bricks: Known for their high thermal conductivity and resistance to chemical corrosion, these bricks are ideal for the intense conditions found in incinerators.
2. Basic Refractories: These are used in environments exposed to basic slags and other corrosive substances. They provide robust protection against chemical attacks.
3. Castables: These refractories can be molded into complex shapes, making them suitable for intricate designs and areas that require custom solutions.
The Importance of Proper Installation
Even the highest quality refractories will fail if not installed correctly. Proper installation is crucial to ensuring that refractories perform as intended and provide the necessary protection. Installation involves precise placement and alignment, as well as attention to details such as joints and seams. Inadequate installation can lead to premature failure, increased maintenance costs, and reduced operational efficiency.
Conclusion
Refractories may not always be in the spotlight, but they are the unsung heroes of high-temperature systems like boilers and incinerators.
By providing essential protection against extreme heat and chemical wear, they ensure the safe and efficient operation of these critical industrial components. Understanding the role of refractories and the importance of proper installation can help optimize performance, reduce maintenance, and extend the lifespan of boilers and incinerators.