Check out our new Substack, Merchandise Trade With Legion
How Ceramic Fiber Can Maximize Efficiency in Refractory Applications?
Explore how ceramic fiber can significantly enhance efficiency in refractory applications by offering superior insulation, high-temperature resistance, and energy savings. Learn about its composition, manufacturing process, and its critical role in modern industrial applications.
ENGLISH
3 min read
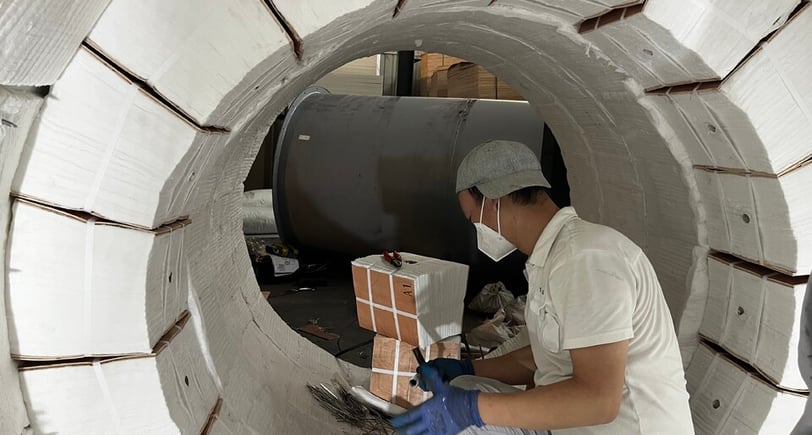
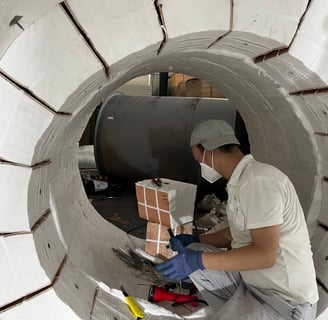
In industries where high temperatures are the norm, the need for effective insulation materials is critical. Refractory applications, in particular, demand materials that can withstand extreme temperatures while minimizing energy loss. One such material that has gained prominence is ceramic fiber. This blog delves into what ceramic fiber is, how it is manufactured, and how it can maximize efficiency in refractory applications.
What is Ceramic Fiber?
Ceramic fiber, also known as refractory fiber, is a type of synthetic mineral fiber made from alumina-silica. It is characterized by its excellent thermal stability, low thermal conductivity, and resistance to chemical attack. These properties make it an ideal material for insulation in high-temperature environments.
Key Properties of Ceramic Fiber:
Thermal Stability: Ceramic fiber can withstand temperatures up to 1400°C (2552°F), making it suitable for a wide range of industrial applications.
Low Thermal Conductivity: It has a low thermal conductivity, which means it effectively insulates against heat, reducing energy loss.
Chemical Resistance: Ceramic fiber is resistant to most chemicals, including acids and alkalis, which ensures its durability in harsh environments.
Lightweight: Despite its high-temperature resistance, ceramic fiber is lightweight, making it easier to handle and install.
How is Ceramic Fiber Manufactured?
The manufacturing process of ceramic fiber involves several steps that ensure the material retains its desired properties.
Raw Material Selection: The process begins with selecting high-purity raw materials, typically alumina (Al2O3) and silica (SiO2). These materials are chosen for their ability to withstand high temperatures and their insulating properties.
Melting: The selected raw materials are melted at temperatures exceeding 1800°C (3272°F) in an electric furnace. The melting process ensures that the materials are thoroughly combined, creating a homogenous mixture.
Fiberization: After melting, the molten material is rapidly cooled and drawn into fibers using either a blowing or spinning process. In the blowing process, high-pressure air is used to blow the molten material into fine fibers. In the spinning process, the molten material is spun into fibers using high-speed rotors.
Collection and Formation: The fibers are collected and formed into various shapes and products, such as blankets, boards, and papers. These products are then heat-treated to enhance their stability and performance.
Finishing: The final step involves cutting, shaping, and packaging the ceramic fiber products according to the required specifications.
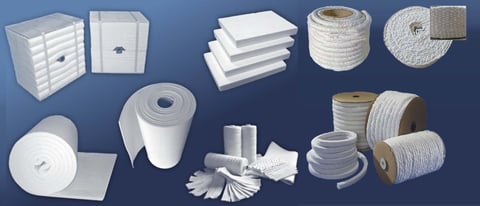
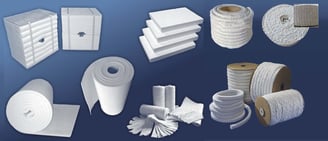
Applications of Ceramic Fiber in Refractory Settings
Ceramic fiber is used in a variety of refractory applications due to its high-temperature resistance and insulation properties. Here are some common uses:
Furnace Linings: Ceramic fiber is often used as a lining material for industrial furnaces, kilns, and boilers. It helps in maintaining high temperatures inside the furnace while reducing heat loss to the surroundings.
Insulation of Piping: In industries where hot fluids are transported through pipelines, ceramic fiber is used as an insulation material to prevent heat loss and ensure the fluid remains at the desired temperature.
Gaskets and Seals: Ceramic fiber is also used in the production of gaskets and seals that can withstand high temperatures, making them suitable for use in engines, turbines, and other high-temperature equipment.
Expansion Joints: In high-temperature environments, materials expand and contract. Ceramic fiber is used in expansion joints to accommodate these changes without compromising the integrity of the structure.
Advantages of Using Ceramic Fiber
The use of ceramic fiber in refractory applications offers several benefits, including:
Energy Efficiency: Due to its low thermal conductivity, ceramic fiber minimizes heat loss, leading to significant energy savings in industrial processes.
Durability: Ceramic fiber's resistance to chemical attack and thermal shock ensures a longer lifespan for refractory linings, reducing maintenance costs.
Lightweight and Easy to Install: The lightweight nature of ceramic fiber makes it easy to handle and install, reducing labor costs and installation time.
Versatility: Ceramic fiber can be shaped into various forms, such as blankets, boards, and papers, making it suitable for a wide range of applications.
Cost-Effective: While the initial cost of ceramic fiber may be higher than some other materials, its long-term benefits, such as energy savings and reduced maintenance, make it a cost-effective solution.
Conclusion
Ceramic fiber has revolutionized the refractory industry by providing a material that not only withstands high temperatures but also enhances energy efficiency and durability. Its unique properties, coupled with its versatility, make it an essential material in industries that require reliable high-temperature insulation. As industries continue to seek ways to improve efficiency and reduce costs, ceramic fiber is likely to play an increasingly important role in refractory applications.